About Jsons foundry Pvt. Ltd.
Established in 1987 by Mr. Ajay and Mr. Sanjay Jadhav, Jsons Foundry Pvt Ltd stands as the inaugural foundry unit, operating independently of any larger organization. With a current manufacturing capacity exceeding 550 tons per month and 80 tons per month Investment casting, the foundry boasts four state-of-the-art facilities equipped with cutting-edge machining capabilities.
Specializing in sand, investment, centrifugal casting units, and machine shop operations, Jsons Foundry Pvt Ltd is known for producing high-quality castings in various grades, including steel, alloy steel, corrosion-resistant stainless steel, super duplex, and high nickel alloys. The foundry delivers fully machined, ready-to-use components with casting capabilities ranging from 500 grams to 1400 kilograms per single piece. Adhering to international standards like ASTM, DIN, BS, EN, JIS, and customer specifications, Jsons Foundry Pvt Ltd is committed to providing prompt and professional responses, aiming to exceed all inquiries and requirements.
Materials
Our teams technical experience allows us to handle wide range of steel alloy
Carbon Steel
ASTM
WCB, WCA, WCC, WC1
DIN
1.0466, 1.0455, 1.0619
Low Temp, Application Steel
ASTM
LCB, LCC, LC3, LC1
DIN
1.0566,
Low Alloy Steel
ASTM
WC6, WC9, C5, C12, C12A G17Cr-Mo. 5-5 & 5-10
DIN
1.7335, 1.7380, 1.7362
Martensitic Steel
ASTM
CA15, CA6NM, CA6NM Class B
DIN
1.4317
Austenitic Stainless Steel
ASTM
CF8, CF8M, CG8M, CF3, CF3M, CF8C, CN7M, CF10, CN3MN, CG3M, CK3MCuN, CU5MCuC
DIN
1.4301, 1.4401, 1.4306, 1.4404, 4.4550
Duplex Steel, Super Duplex
ASTM
1B, 2A, 3A, 4A, 5A,6A
DIN
1.4501, 1.4462
Nickel Base Alloy
ASTM
Monel (M35-1, M35-2, M30C), Hastelloy C and B, Cu5MCuC, CN3MN, CT40, CZ100, CW12MW, CW6M, CX2M, CN7M, CK3MCuN
Nickel Aluminium Bronze
ASTM
C95500, C95800, C95820
High chrome
A532 Type III
Facilities
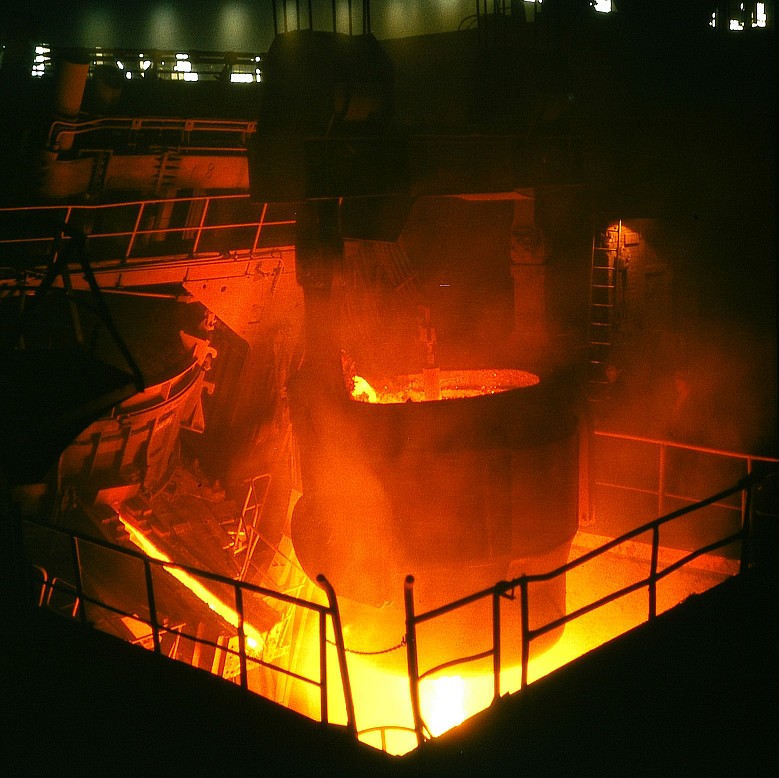
Induction Furnace
Melting facilities with 1MT x 2 Nos, 2MT x 2Nos, 500KG x 1 Nos , 300 KG x 2 Nos and 150 KG x 1 Nos medium frequency induction furnace
Simulation Software
Simulation software to check the soundness of casting before pouring.
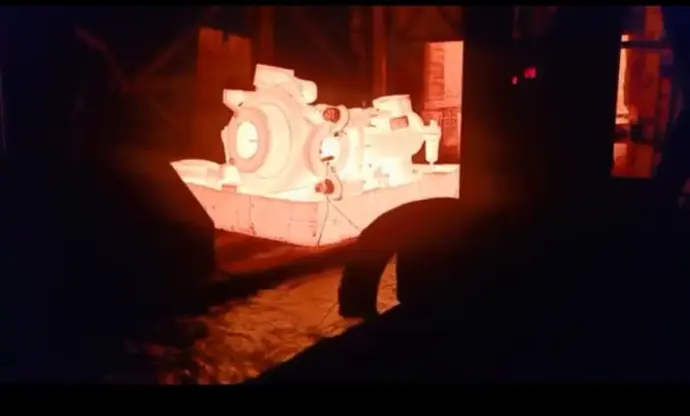
Heat Treatment
Heat Treatment furnace - 03 Nos of Bell Type Gas Fired heat treatment furnace with quenching facility
NABL Lab
Set Standards for testing and calibration laboratories to ensure they meet specific criteria for quality standards accuracy and reliability
Facilities for Testing
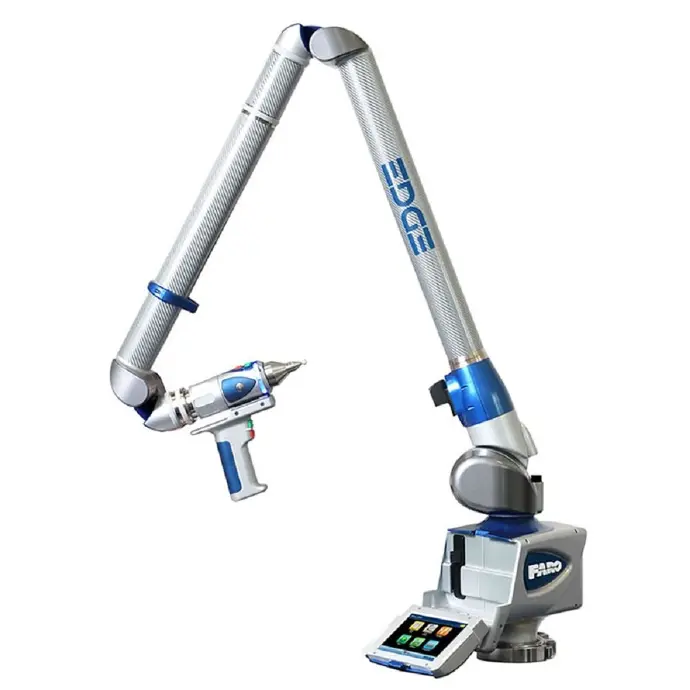
Scanning by Faro arm
Offering precise and efficient scanning solutions that enhance quality control and streamline production processes.
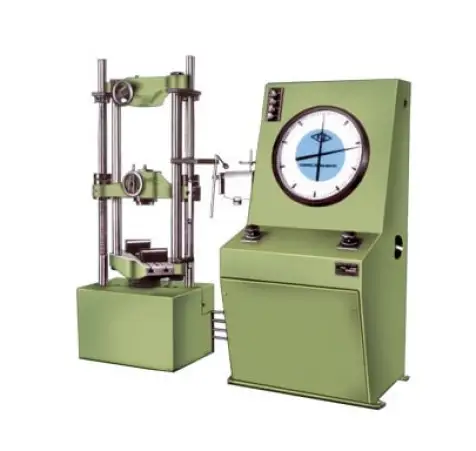
U.T.M
Model FSA model TUV 400
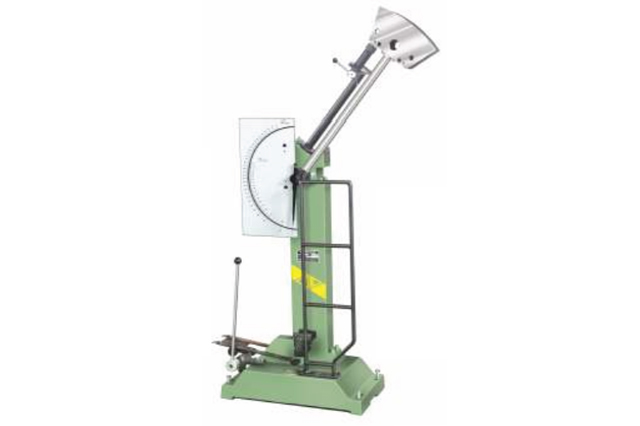
Impact Testing
Impact test facility done upto -196 degree celcius
Radiography Enclosure
In Total 6 Enclosures
4 Nos Iridium, 2 Nos Cobalt
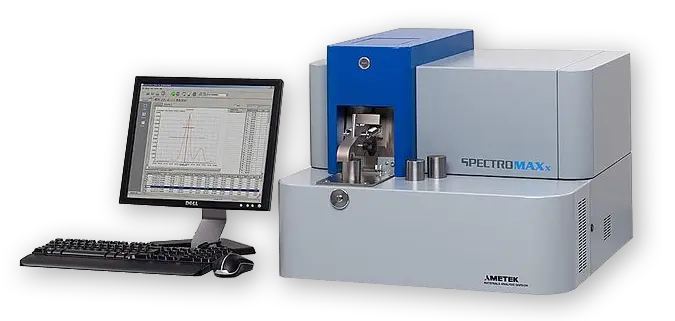
Spectrometer
Spectro analysis of 30 Element- Cu,Ni,Fe Base
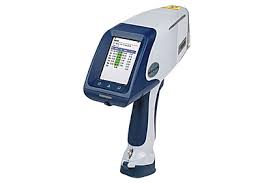
- ASTM G48 METHOD A/B/C/E
- ASTM A923 METHOD-A/B/C
- ASTM A262 Pr- A/B/C/E/F
- ASTM G28 METHOD-A
- ASTM A923 METHOD A
- ASTM E407
- ASTM A262 Pr-A
- MICROSTRUCTURE ANYLISIS AS PER
- ASM Handbook Vol-IX
- ASTM E112
- ASTM E562
- ASTM E1351
Non-Destructive Testing
- MP Test - Yoke Type, Probe Type
- DP Test - Solvent Base, water Washable
- UT Test - Radiography Enclosure - Linac -01, IR-01, Co-03 qty
Quality Control
- Softcast Simulation
- Faro Edge Arm for 3D Scanning and GD & T
Laboratory
- Spectrometer with 32 channels
- Ferritoscope
- Digital Hardness Tester
- Impact Testing Machine
- Universal Testing Machine
- In-Situ
Simulation Software
By simulating various casting techniques, such as sand casting or investment casting, this software allows for the optimization of Mold design, gating systems, and process parameters. Through virtual experimentation, potential defects like porosity, shrinkage, and distortion can be identified and mitigated prior to physical production, saving both time and resources. Furthermore, simulation software enables engineers to explore alternative designs and materials, facilitating innovation and continuous improvement in casting processes. Overall, the integration of simulation software in casting manufacturing empowers manufacturers to achieve higher quality, reduce costs, and accelerate time-to-market for their products.
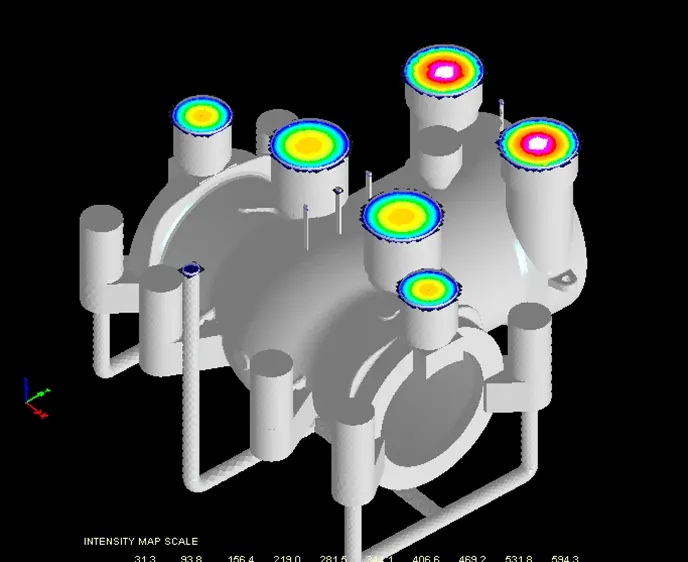
Gate Valve Body
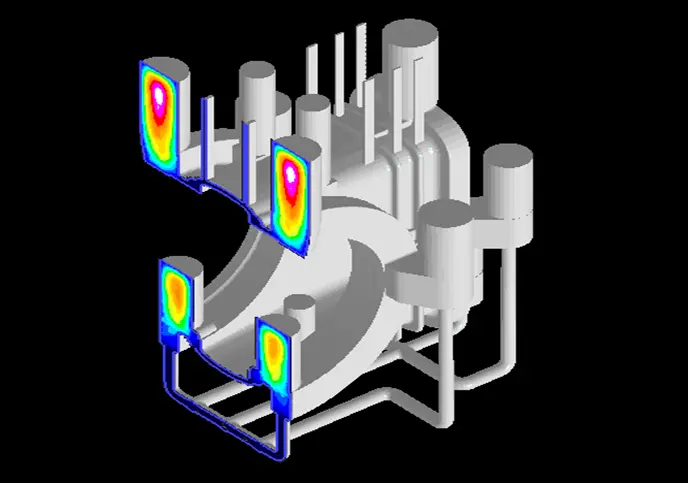
Gate Valve Body
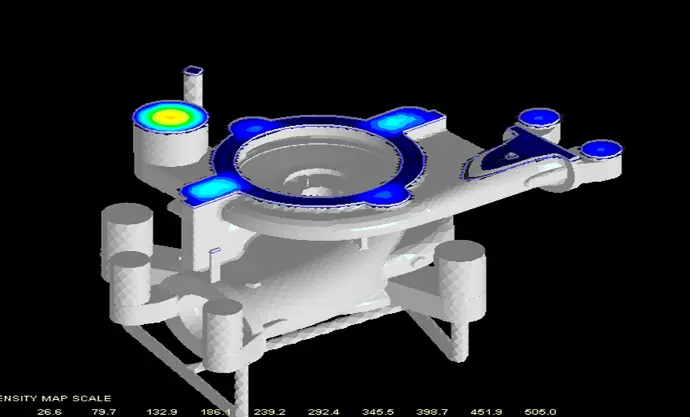