About
Western Precicast Pvt Ltd, a distinguished name in Big Size casting and machining. Including an AOD Furnace with a capacity of 12 MT, Induction Furnaces ranging from 4 MT to 6.5 MT, and Heat Treatment Furnaces with capacities of 8 MT and 14 MT. Utilizing advanced simulation software, we ensure precision and efficiency in our processes.
In our fully equipped machine shop, we have a comprehensive range of machinery, including Travisan, VMC, HBM, and more, enabling us to meet diverse machining requirements with excellence.
At Western Precicast, quality is our commitment. Our NDE/NDT facilities include MP, DP, and UT tests, along with radiography capabilities using Linac (6MeV), Iridium (1 enclosure), and Cobalt (3 enclosures). We employ a state-of-the-art spectrometer with 32 channels for precise composition analysis.
For quality inspection to machined castings, facilities further include a Faro arm for 3D scanning and GDNT with a 2.7 m capacity.
For Mechanical testing - UTM and Impact Testing Machines, and various hardness testing equipment
Other testing equipment - Ferritoscope POSITIVE MATERIAL IDENTIFICATION (PMI), In-Sutu Metallographic equipment to check Microstructure on the Job.
At Western Precicast, we take pride in our advanced facilities and unwavering dedication to delivering high-quality, precision-engineered products that meet and exceed industry standards & customer’s satisfaction.
Our Certifications
Driving Growth: Western Precicast's Annual Tonnage Production
At Western Precicast, our commitment to excellence is evident in the impressive yearly tonnage produced through our manufacturing processes. Each year, our state-of-the-art facilities tirelessly churn out substantial tonnages of high-quality products, reflecting our dedication to meeting the demands of our clients and industry standards. Our unwavering focus on efficiency, innovation, and precision allows us to consistently achieve remarkable production volumes while maintaining exceptional quality standards. The accompanying bar chart visually depicts the upward trajectory of our yearly tonnage production, showcasing our continuous growth and unwavering commitment to excellence in manufacturing.
Facilities
Induction Furnace
Melting facilities with 4MT, 5MT and 6.5 MT medium frequency induction furnace
Decarburization Unit
Argon Oxygen Decarburization Unit (AOD) - 12MT
Simulation Software
Simulation software to check the soundness of casting before pouring.
Heat Treatment
Heat Treatment furnace - 03 Nos of Bell Type Gas Fired heat treatment furnace with quenching facility
Machine Shop
full fledge machine shop with 7 Nos Trevision Machine - CNC-VTL /HBM /VMC / RADIAL drill
Omega Sand Mixer
Qty- 2 in molding shop and 1 in core shop. Molding 20 ton per hour Core- 10 ton per hour.
Facilities for Testing and Inspection
Scanning by Faro arm
Offering precise and efficient scanning solutions that enhance quality control and streamline production processes.
U.T.M - Model FSA model TUV 400
Impact test facility done up to -196 degree Celsius.
Radiography Enclosure
09 Radiography Enclosure - 5 Nos Co-60, 3 Nos Ir-192 & LINAC - 6Mev
Spectro - for Chemical Analysis
2 Nos Spectro and all in house chemical and mechanical testing facilities.
Spectro - In Nickel & Nitrogen
PMI - To check Chemical on Job
Impact Testing
Impact test facility done upto -196 degree celcius
Corrosion Test
- ASTM G48 METHOD A/B/C/E
- ASTM A923 METHOD-A/B/C
- ASTM A262 Pr- A/B/C/E/F
- ASTM G28 METHOD-A
Metallography
- ASTM A923 METHOD A
- ASTM E407
- ASTM A262 Pr-A
- MICROSTRUCTURE ANYLISIS AS PER
- ASM Handbook Vol-IX
- ASTM E112
- ASTM E562
- ASTM E1351
Simulation Software
By simulating various casting techniques, such as sand casting or investment casting, this software allows for the optimization of mold design, gating systems, and process parameters. Through virtual experimentation, potential defects like porosity, shrinkage, and distortion can be identified and mitigated prior to physical production, saving both time and resources. Furthermore, simulation software enables engineers to explore alternative designs and materials, facilitating innovation and continuous improvement in casting processes. Overall, the integration of simulation software in casting manufacturing empowers manufacturers to achieve higher quality, reduce costs, and accelerate time-to-market for their products.
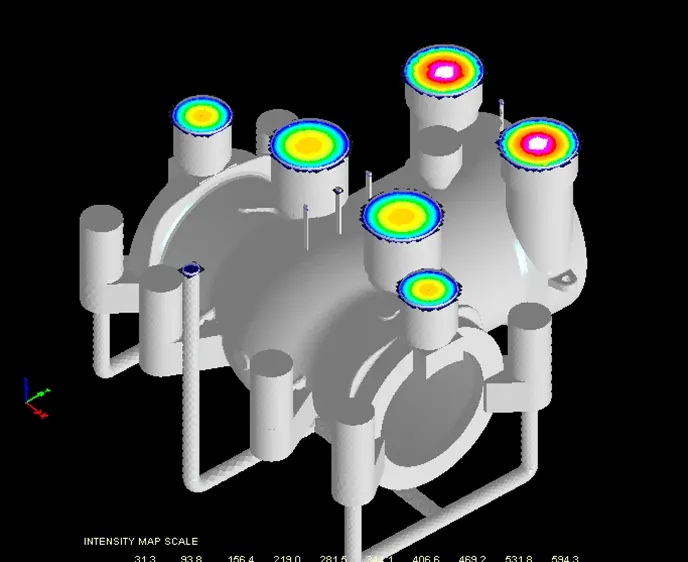
Gate Valve Body
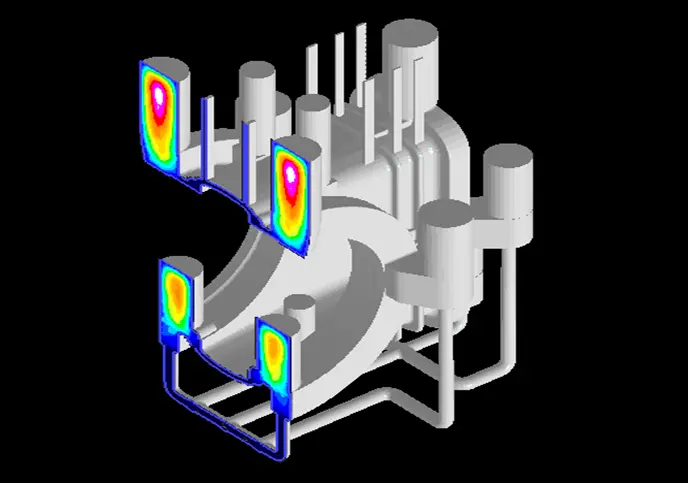
Gate Valve Body
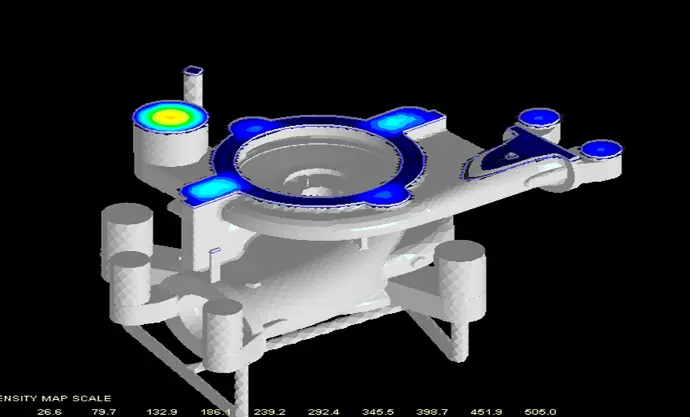
Pump Casting
Facilities Available for Quality Control
Non-Destructive Testing
- MP Test - Yoke Type, Probe Type
- DP Test - Solvent Base, water Washable
- UT Test - Radiography Enclosure - Linac -01, IR-01, Co-03 qty
Quality Control
- Softcast Simulation
- Faro Edge Arm for 3D Scanning and GD & T
Laboratory
- Spectrometer with 32 channels
- Ferritoscope
- Digital Hardness Tester
- Impact Testing Machine
- Universal Testing Machine
- In-Situ
Machine Shop
Western Machine Shop Capacity
Trevisan (DS600, DS900,DS1000) | 07 |
Vertical Milling Center | 06 |
Vertical Turning Machine | 14 |
Horizontal Boring Machine | 05 |
Horizontal Milling Machine | 04 |
Radial Drilling Machine | 02 |
Hydro Testing Machine | 01 |